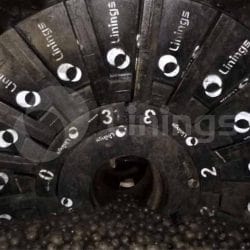
Its known that the caps of a mill are not decisive for grinding, as shell liners can be to a certain extent. However, it is important that the cap liners comply as far as possible with a stable duration time, which may be equal to the useful life of the shell liners or half of their useful life. In this way, plant stoppage interruptions due to cover replacement are avoided. In a 12x16 all-steel lined ball mill, the customer had problems with their caps that he had to make continual changes to, as the life of the feed cap was around 3 months and the discharge cap around 3 months. 6 months. Linings developed its composite cover model for this client, which has been able to deal with the problem of duration: supply cover between 5 and 6 months, discharge cover around 11 months. This has meant a 90% increase in the duration of their caps, thus having fewer stops during their campaign. In addition to this, as the liners are lighter than pure steel designs, a reduction in man-hours per installation and lower energy consumption is achieved.